Our Services
Radiography
SafeRad™ the World Leaders of Close Proximity Radiography
Click on the following links to Download more information
- SafeRad™ Flyer
- GammaBlok™ Flyer
- SafeRad™ Presentation
- GammaBlok™ Presentation
- SafeRad™ Se75 Exposure Container Data Sheet
- SafeRad™ Selenium 75 Data Sheet
SafeRad™ offer a range of Radiography Services from Computed Radiography, Digital Radiography and Conventional Film Radiography for both X-Ray and Gamma-Ray.
We have purpose built facilities at all our offices for loose spooling and welder qualification test pieces. We also offer on site Radiography with our world leading SafeRad™ Radiography System utilising SE-75 sources giving far superior quality than Ir-192. Enabling the client to always meet construction code requirements for sensitivity at all times.
Radiography can either be carried out in the Close Proximity mode or the conventional mode without the use of other equipment, one system-all methods, at the same cost as what other companies would charge you for conventional radiography using Ir-192.
SafeRad™ manufacture all of their own equipment so there is no middle man, which allows us to keep our costs down.
We save the clients thousands of Dollars and hundreds of thousands of Dollars on long term projects.
We also have purpose built Ir-192 equipment for heavy wall pipework for onsite Radiography Projects where small barriers of 2 metres or less are required.
We have state of the art processing facilities and portable darkrooms for onsite Radiography.
All SafeRad™ Technicians are fully trained and competent in the use of the SafeRad™ Radiography system and follow a rigorous training program to become qualified in its use.
No other companies can compete with SafeRad™ in this field, we are the industry Leaders and the World Experts in Close Proximity Radiography.
As well as the World Leading SafeRad™ System
SafeRad™ also offer a full range of Radiography Services
Digital (DR) / Computed Radiography (CR) and X-Ray see below for Information
Corrosion Monitoring Images showing wall thickness measurement
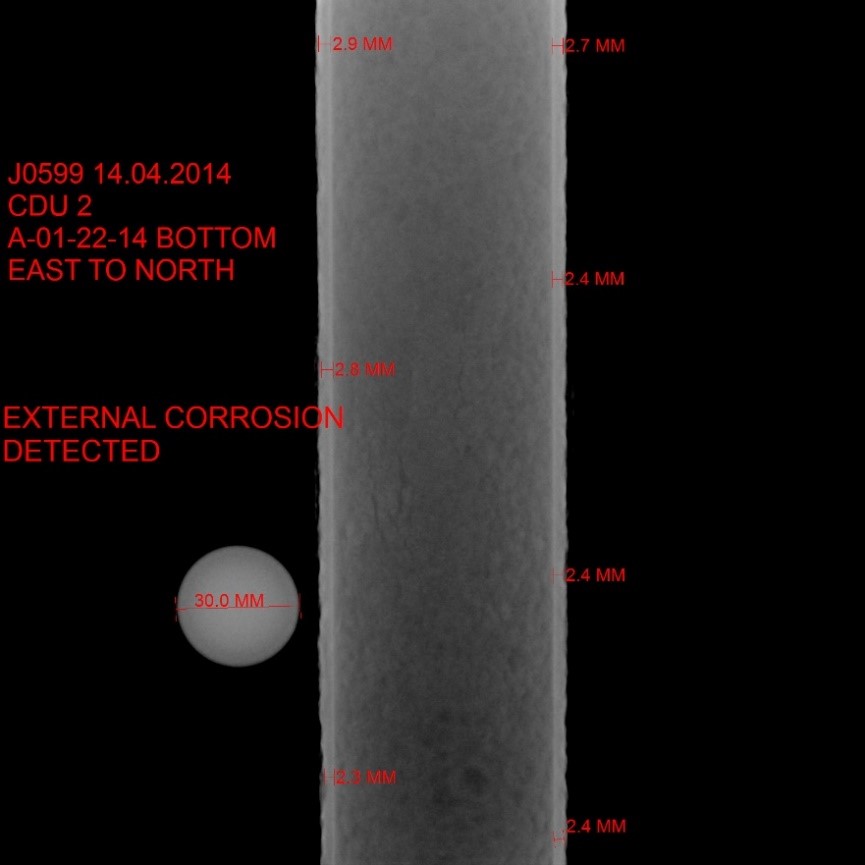
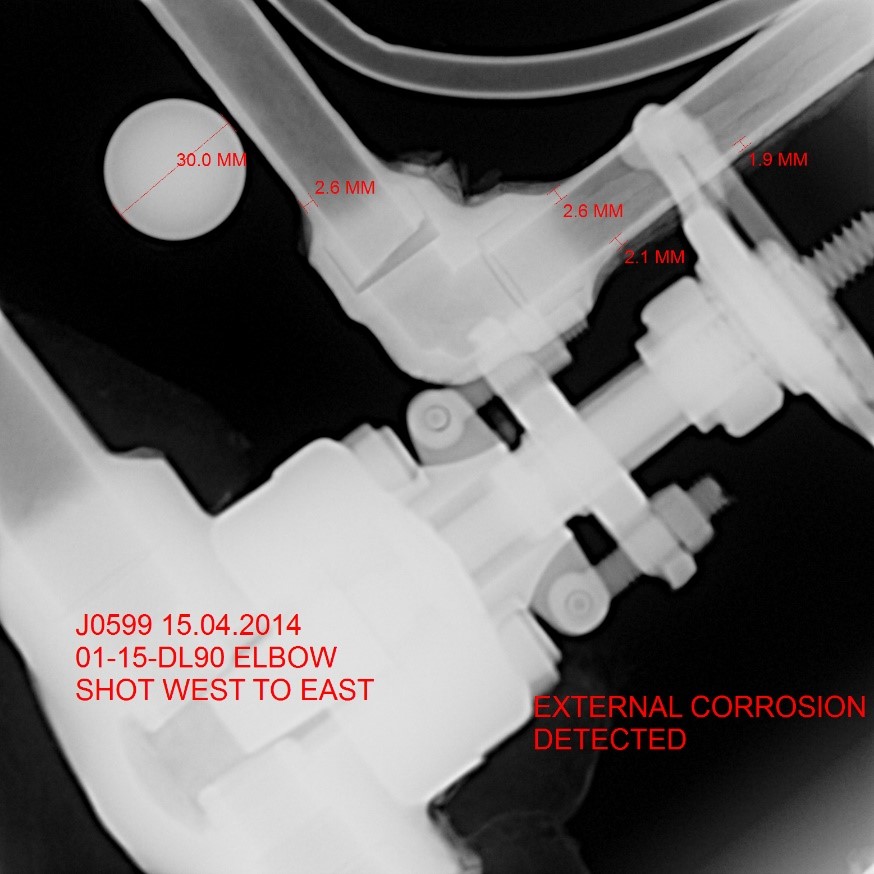
Images showing DR and CR capabilities of Software Enhancement Tools
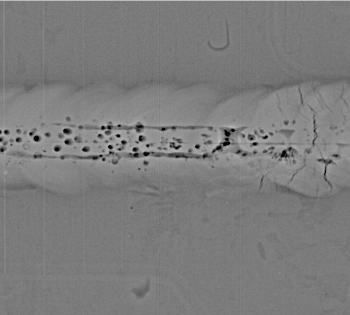
Branch Weld enhanced with software tools showing defects clearly

Branch Weld enhanced with software tools showing defects clearly
Digital Radiography (DR)
Digital Radiography (DR) is the most advanced X-ray and Gamma-Ray technology available.
Instead of X-ray film, digital radiography uses a rigid digital image capture device known as a Digital Detector Array (DDA) Panel. This gives advantages of immediate image preview and availability, elimination of costly film processing steps, a wider dynamic range which makes it more forgiving for over and under exposure as well as the ability to apply special image processing techniques that enhance overall display quality of the image.
The Digital Detector Array (DDA) panel produces the best image quality in the market allowing for the highest level of detection. The unique combination of fast image generation, software enhancement and analysis tools, as well as efficient operation, dramatically speeds up the inspection process, increasing NDT profitability.
Portability enables fast set up under any conditions, at any location – whether it is on site, outdoors or in the laboratory. With the super thin DDA imager and integrated wireless options, you can conduct X-ray and Gamma-Ray inspections anywhere, without cables. Highest quality, razor sharp images are created with a click of a button enabling you to conduct an analysis on your laptop immediately, on site.
Modular Design: Easy setup, dual use, in the Laboratory, or in the field. Compatible with portable Pulsed, Constant Potential & High Frequency X-ray sources, as well as Isotopes. Full synchronization with various X-ray sources.
Corrosion Monitoring: Automatic Wall Thickness Measurement, Precise Wall Thickness & Defect Measurement Tools. Facilitates fast and exact (calibrated) multiple measurements.
Image on Screen within Seconds: No re-positioning results shown immediately. No developing, no scanning and no chemicals.
Image Share: Images are stored electronically and can be shared around the world for viewing by your clients with free viewing software.
SafeRad™ have Completed a number of Projects Australia wide with Digital Radiography.
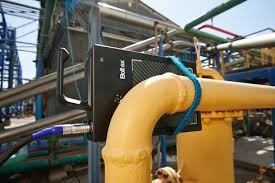
Digital Radiography Plate Setup
Computed Radiography (CR)
CR is the abbreviation for Computed Radiography. It is the use of a Phosphor Imaging Plates to create a digital image known as the CR process. CR uses a cassette-based system like analogue film.
CR offers all the same Software advantages as Digital Radiography but uses a flexible Image plate rather than a rigid Digital Panel.
SafeRad™have completed a number of projects in Australia and Worldwide with Computed Radiography.
X-Ray Radiography
SafeRad™ have purpose-built x-Ray bays at all there facilities to service local Industry for spooling and welder qualification works for all clients.
We also offer a full range of onsite X-Ray tubes such as Directional, Panoramic and Pipeline Crawler systems (Crawler Systems available for project works).

300KV Directional X-Ray Set

Pipeline Works

X-Ray Crawler System for Pipelines
Film Digitisation
The Film Digitising System is an all-in-one imaging solution developed exclusively for the radiographic inspection industry. It easily transfers the industrial X-Ray film into a digital image for storage and management which makes it convenient to view and share.
It is a cost-effective way to digitise and archive radiographic film.
With just a simple and fast connection, you are able to transfer physical data into digital format.
SafeRad™ offer state of the art Film Digitisation equipment for archiving of X-Ray film Radiographs.
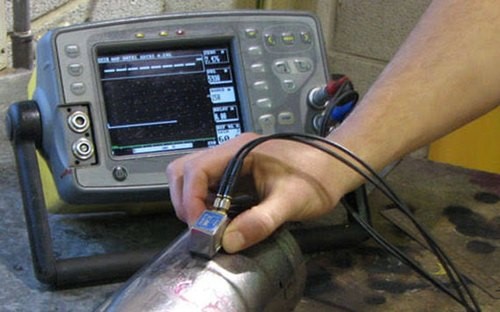
Phased Array is widely used in Non-Destructive Testing (NDT).
Phased Array is an advanced NDT method that is used to detect discontinuities i.e. cracks or flaws and thereby determine component quality. Due to the ability to control parameters such as beam angle and focal distance, this method is very efficient regarding the defect detection and speed of testing. The technology uses multiple ultrasonic elements, multiple angles and electronic time delays to create beams that can be steered, scanned, swept, and focused electronically for fast inspections and full data storage.
Apart from detecting flaws in components, phased array can also be used for wall thickness measurements in conjunction with corrosion monitoring testing.
Phased Array gives accurate cross-sectional views of internal structures at fast inspection speeds. Phased Array technology provides precise measurement with the most reliable results.
SafeRad™ offer experienced Level 2 ISO 9712 Technicians for both weld scan and thickness inspection for corrosion monitoring and use the latest equipment in this technology.
Olympus OmniScan X3
The OmniScan X3 flaw detector is a complete phased array toolbox. Innovative TFM (total focusing method) delivers outstanding images that help inspectors identify flaws with confidence while powerful software features and simple workflows help you get to work fast.
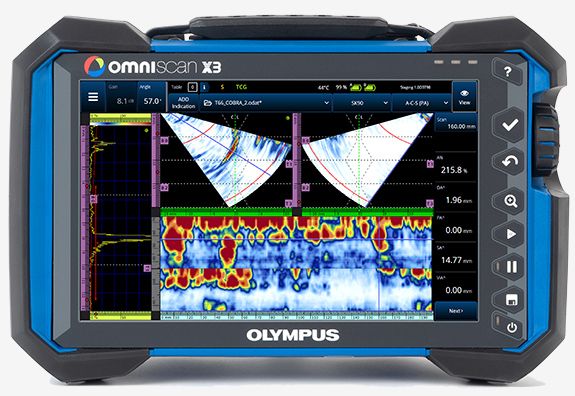
The OmniScan X3 offers:
- Twice as fast as the OmniScan MX2 (pulse repetition frequency).
- Single TOFD menu for accelerated workflow.
- Improved fast phased array calibration minimizes frustration and increases time efficiency.
- 800% high amplitude range reduces the need to rescan.
- Onboard Dual Linear Array and Dual Matrix Array probe support.
- Accelerates setup creation.
SafeRad™ offer experienced Level 2 ISO 9712 Technicians
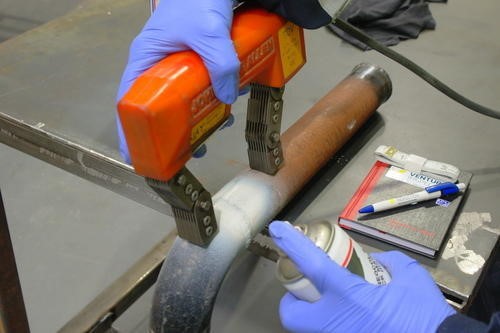
SafeRad™ offer experienced Level 2 ISO 9712 DPI Technicians.
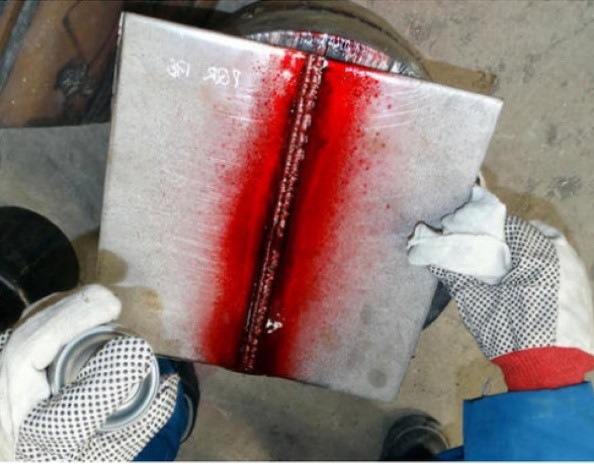
Proceq’s Equotip enables portable hardness inspection of almost any object, polished parts and heat-treated surfaces. The hardness measurements are made by using the dynamic rebound testing method according to Leeb, the static Portable Rockwell hardness test and the Ultrasonic Contact Impedance (UCI) method. The rugged Swiss-made metal NDT hardness testers are designed for portable hardness testing in the lab, in the workshop, at production facilities or on site.
SafeRad™ offer both Equotip 3 and the new Equotip 550 UCI Tester.
UCI Method
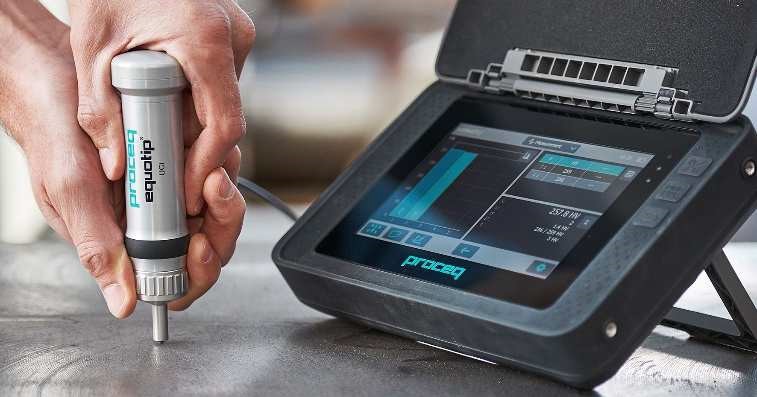
Rebound Method
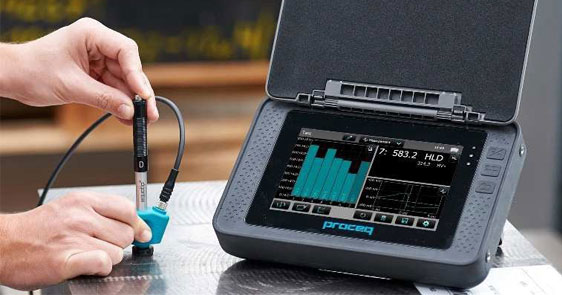
SafeRad™ offer a range of portable PWHT solutions with trained and Experienced Technicians in this method and have completed a number of major projects over the years.
Typical PWHT Setup
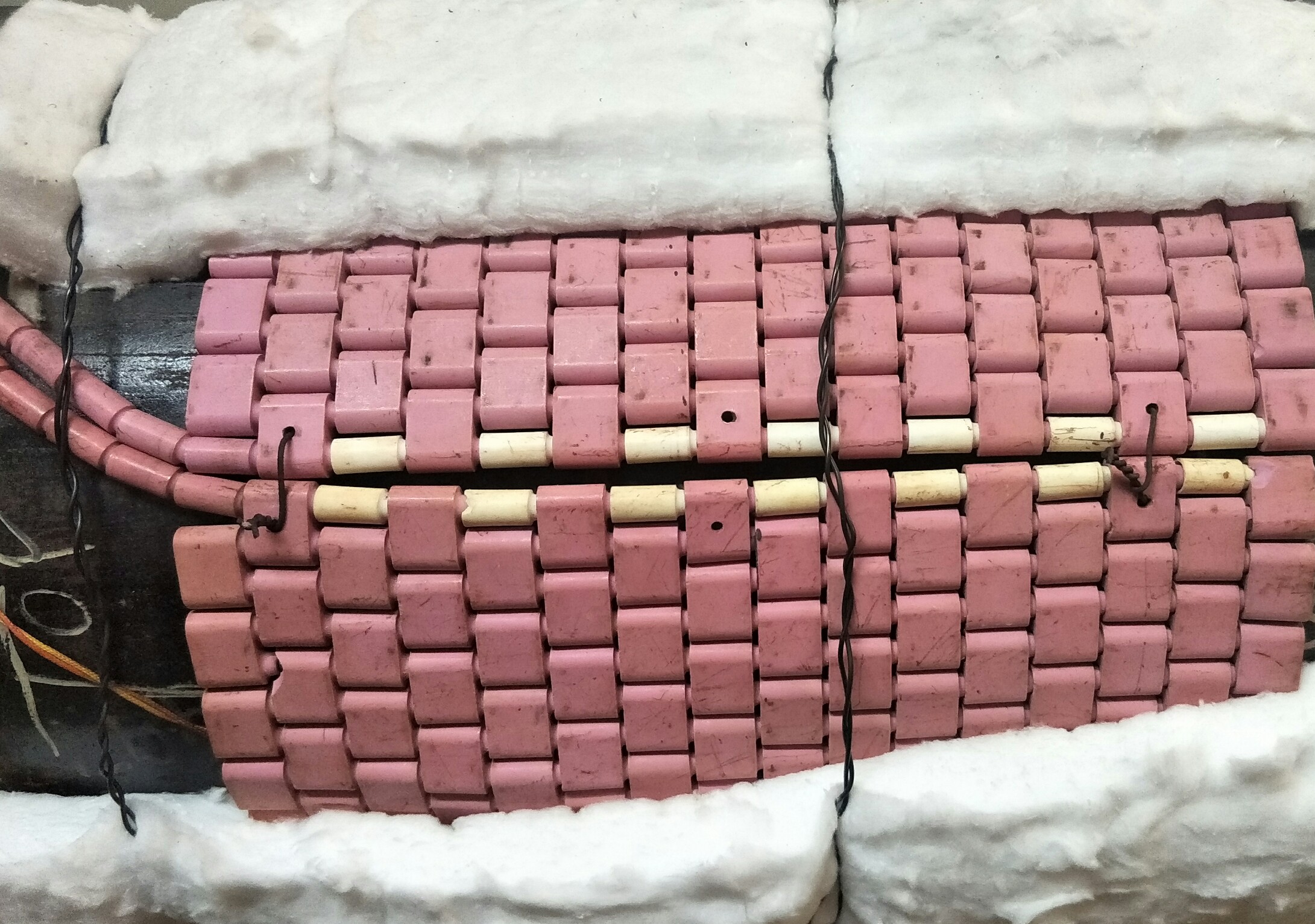
Portable PWHT Equipment
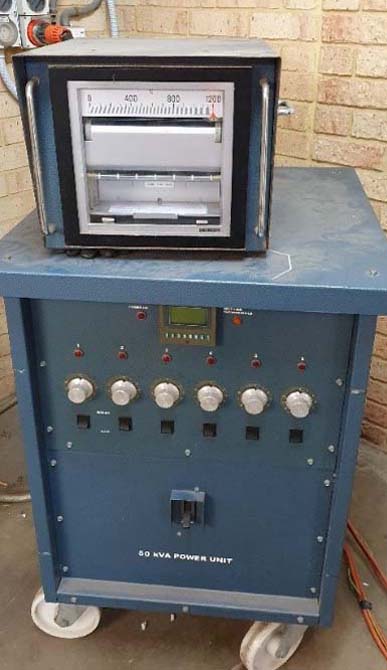
X-ray fluorescence (XRF) is the emission of characteristic “secondary” (or fluorescent) X-rays from a material that has been excited by being bombarded with high-energy X-rays or gamma rays. The phenomenon is widely used for elemental analysis and chemical analysis, particularly in the investigation of metals, and other materials.
SafeRad™ offer Trained and Olympus Certified Technicians in the use of The Olympus Delta and Vanta Analyzers.
Delta XRF Analyser
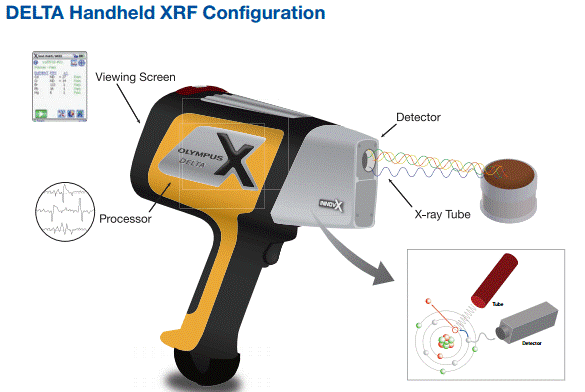
Vanta XRF Analyser
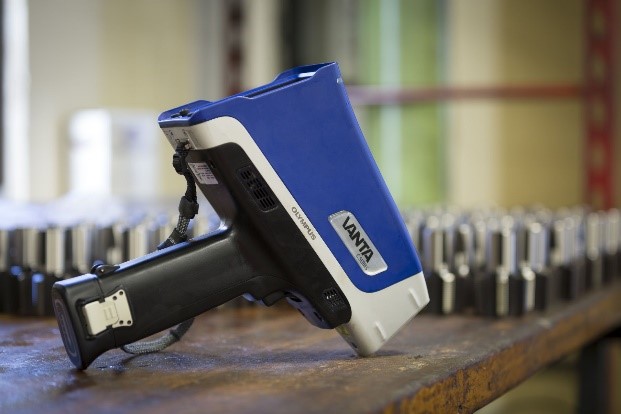
Analyse carbon content in carbon and stainless steels, utilizing the technique of handheld laser induced breakdown spectroscopy (HH LIBS). The method specifies the SciAps Z-200 C+, the world’s only handheld analyser capable of analysing carbon content in alloys.
Sciaps Z-200 Series Analyser
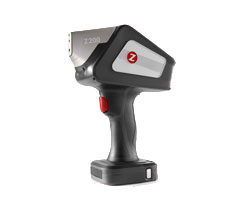
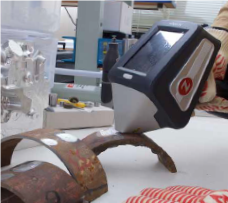
Alternatively, if the ferrite content is too high, the weld may be weaker and corrode. To address the need to measure the amount of ferrite in a sample the Welding Research Council introduced the Ferrite Number (FN) as a standardised value which related to the ferrite content of an equivalently magnetic weld metal.
The volume percentage of ferrite can be estimated as about 70% of the FN but the relationship depends upon the type and origin of the stainless steel used and the measurement technique.
The Diverse Ferrite Metre MF300F+ measures the Ferrite number (FN) of austenitic and duplex stainless steel weld material. It has a probe that is sensitive to ferrite content in a 10 mm area to a depth of approximately 1 mm. The instrument is calibrated using the secondary world standards held at The Welding Institute.
All 16 standards are used in the calibration giving an instrument with a measurement range from 0 to 115 FN. Transfer standards are supplied with the instrument allowing performance to be verified at any time. A variety of measurement modes are supported to ensure that good repeatable measurements can be made.
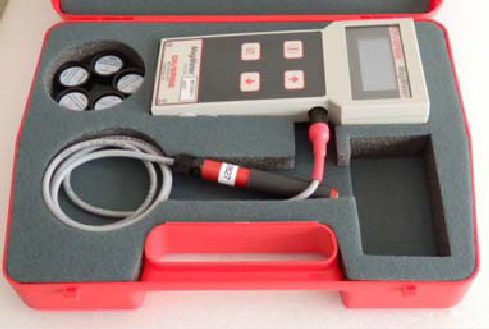
Visual Camera inspection is an easier and less expensive method for welding inspection. It is the first step in checking for any welding anomalies; visual inspections are required before and after weld-joints are completed. It is difficult to carry out a visual inspection on internal weld spots and as such you will need an inspection camera to access the hard to reach, smaller diameter piping.
‘SafeRad™’s remote visual camera inspection system is designed for the modern industrial inspection environment. We offer portable, battery type, wired and wireless inspection cameras which provide a real-time colour image and also provide video for examining welds inside pipes and the structural framework of various diameters. A viewing angle of 360-degrees and a 180-degree tilt probe means the camera is suitable for inspecting all your weld surface irregularities and ensuring a good welding finish.
Useful for Debris inspection of pipework as well as weld root analysis.
See PowerPoint for Camera details
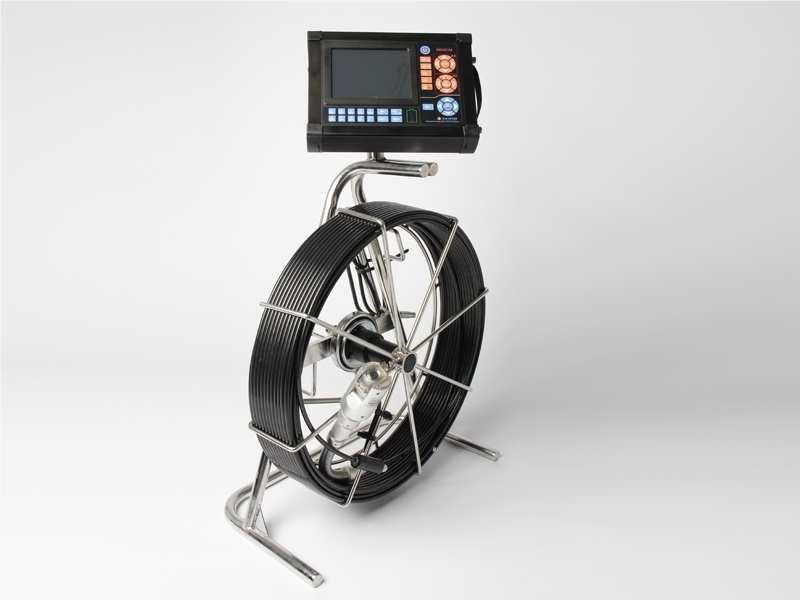
Stages of Typical On-Site Setup
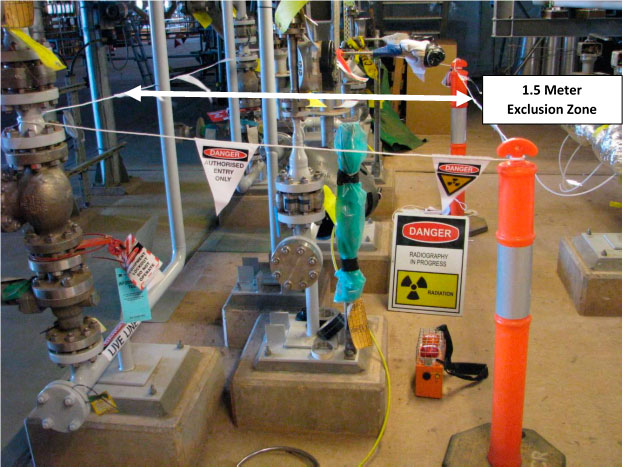
SafeRad™ are conducting Close Proximity Radiography throughout the site to determine ball valve orientation.
This activity is different from Conventional Radiography. The method uses different radiation sources and radiation shielding to reduce radiation scatter and emit a low level of radiation energy.
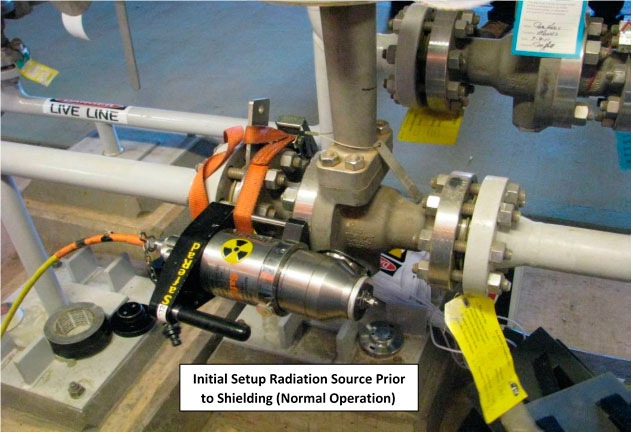
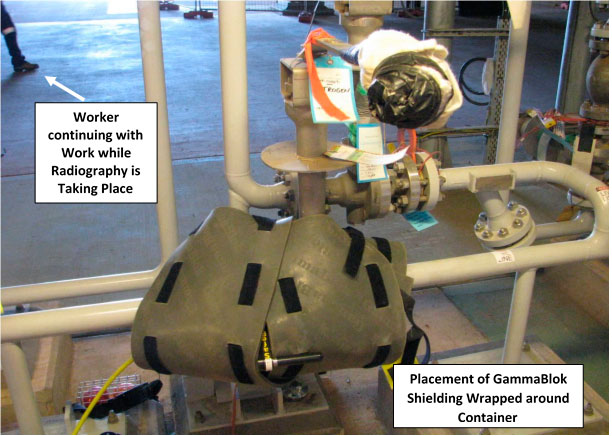
Conventional Radiography is unshielded and emits scatter radiation outward; hence previously larger exclusion zones were required.
Conventional Radiography and legislative requirements permit the maximum radiation energy to be 20 microsieverts per hour in Western Australia and 25 microsieverts per hour in all other States and territories at the boundary during operation.
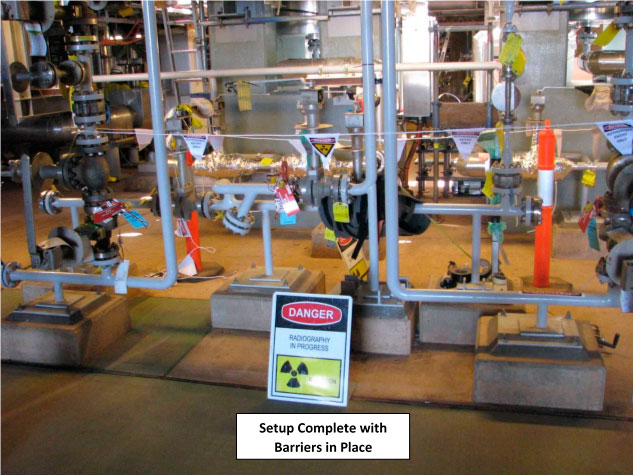
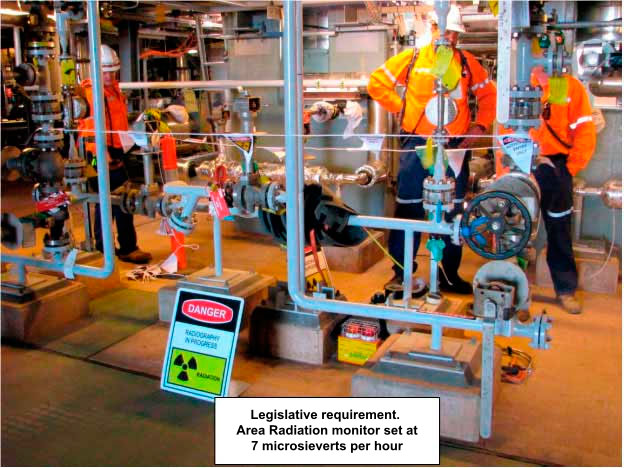
The SafeRad™ Close Proximity Radiography system reduces emitted radiation to between 0.5 & 5 microsieverts per hour at the boundary during operation (this is equal to or less than the normal background radiation emitted from the sun in the Pilbara region). This means there is a reduction in emitted radiation of at least 5 times the national allowable exposure limits but up to 50 times less than the allowable limits are commonly achieved. This equates to an increased level of safety for the technicians involved in the activity, the environment and all other project personnel.
SafeRad™ are conducting Close Proximity Radiography throughout the site to determine ball valve orientation.
This activity is different from conventional Radiography.
The method uses different radiation sources and radiation shielding to reduce radiation scatter and emit a low level of radiation energy.
Conventional radiography is unshielded and emits scatter radiation outward; hence previously larger exclusion zones were required.
Conventional Radiography and legislative requirements permit the maximum radiation energy to be 20 microsieverts per hour in Western Australia and 25 microsieverts per hour in all other States and territories at the boundary during operation.
The SafeRad™ Close Proximity Radiography system reduces emitted radiation to between 0.5 & 5 microsieverts per hour at the boundary during operation (this is equal to or less than the normal background radiation emitted from the sun in the Pilbara region). This means there is a reduction in emitted radiation of at least 5 times the national allowable exposure limits but up to 50 times less than the allowable limits are commonly achieved. This equates to an increased level of safety for the technicians involved in the activity, the environment and all other project personnel.